The differential housing is a tractor component manufactured by John Deere (see Figure 1). The material is ductile iron N550B06, which requires heat treatment and quenching to be the crest, bottom and sides of the head of the six teeth (see Figure 2). The effect to be achieved is that the surface (ie, the top of the tooth, the bottom of the tooth, the sides of the tooth) has a hardness of 40-50HRC, and the hardness of 2mm (ie, the secondary surface) below the surface is ≥35HRC.
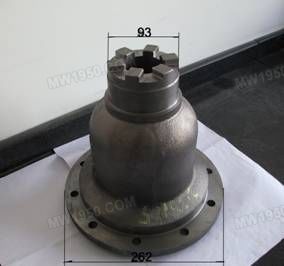
Figure 1 actual workpiece
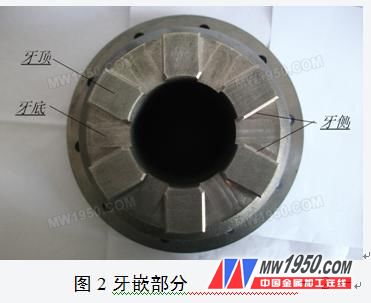
In the past, the local heating of the salt furnace was used. The 75KW furnace can only heat two pieces. It needs to be isothermally heated for 20 minutes to be sterilized and then dip-quenched. In addition to the process of air furnace heating, quenching and transfer, the average daily quenching of 20 pieces can not meet the production needs. And due to manual operation, the distribution of the hardened layer is not well controlled. Many units have tried to use induction heating and quenching. Although the productivity has been improved, the quenching stress tends to cause arc cracking and the scrap rate is high.
In early 2009, Tianjin Shengtaida Company accepted the entrustment from customers and began to test the heat treatment process of the differential case with the medium frequency induction heating power supply and the matching numerical control quenching machine produced by Tianjin Tiangao. After repeated trials, the induction heating and automatic control quenching procedure of the differential housing were finally determined. Among them, the power supply is determined, and the voltage and current double closed-loop adjustment control is adopted to ensure the stable output of the power supply; the matching is automatically tracked at 4KHZ to adapt to the workpiece state; preheating, heating timing, transfer timing, automatic spray quenching liquid timing. The worker only needs to press the start button, and a differential case is automatically quenched for 95 seconds, and 120 pieces can be quenched in half a working day. The efficiency is 12 times that of the salt furnace heating and quenching, and the electricity consumption is about 1/4 of the salt furnace. It is superior to salt furnace in environmental protection and cleaning heat treatment. In terms of heat treatment effect, due to the automatic control of induction heating, the heating time, the transfer time, and the cooling rate are consistent, and the mass dispersion is lowered. Moreover, due to the different mechanism of induction heating and salt furnace heating, the rapid heating and skin effect make the workpiece obtain the ideal hardened layer distribution and surface structure (see Figure 3, Figure 4), and have a good hardness gradient (see Table 1). ). Thereby meeting the performance of the workpiece.
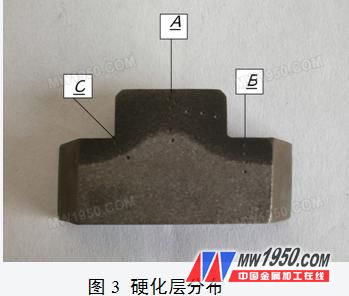
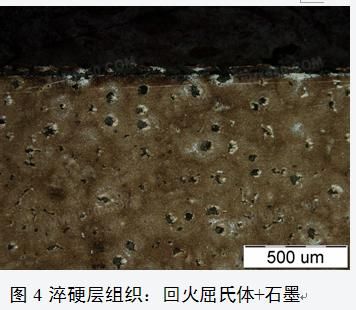

The difficulty of induction heating quenching of the differential housing is how to avoid quenching cracks. Through practice, we believe that the following points are effective measures to avoid cracks:
1. Considering the slow heat conduction of cast iron, the preheating program is added.
2. The root must be heated to more than 3mm.
3. Select a suitable quenching cooling medium.
4. The angle of the quenching liquid spray must ensure that the top, bottom, side and root are simultaneously cooled, especially the roots should not be slow.
After the induction heating and quenching of the differential housing, the time span was 4,000 pieces in spring, summer, autumn and winter, and 100% of the magnetic powder was inspected. No arc cracking was found.
In summary, we believe that the heat treatment of the ductile iron differential shell is changed from manual furnace quenching by salt furnace heating to medium frequency induction heating program-controlled quenching, which reduces energy consumption and is environmentally friendly, and greatly improves production and processing efficiency. The desired hardened layer distribution and performance are obtained.
At the time when the national heat treatment industry is discussing the goals of the US Heat Treatment 2020, the development of heat treatment is the main line of high-quality, high-efficiency, low-energy, clean, environmentally friendly and intelligent. Our practice is in line with the trend. From our case, we can promote the heat treatment of cast iron parts in other vehicle industries, and we will achieve good results.
references
[1] Zhu Yunce. Sustainable materials and heat treatment technology for the automotive industry. Metal Heat Treatment, 2010, 35(1): 19-22.
Welded Wire Mesh
Welded Wire Mesh,Galvanized Welded Wire Mesh,Stainless Steel Welded Wire Mesh
Yongzhong Wiremesh Co., Ltd. , http://www.hbwires.com