The hydraulic impact crusher is a mechanical equipment that uses the impact energy to break the ore. The target equipment has the characteristics of high crushing ratio, high efficiency, low energy consumption, regular grain size, and selective crushing. Therefore, although it appeared later, it has developed rapidly.
It has been widely used in the middle and fine crushing of various ores in the building materials "target=_blank> building materials, coal, chemical engineering and engineering industries. Due to the working principle, the hammers and counter-attacks of the hydraulic impact crusher are all The wear of the parts is more serious and difficult to solve, so it is rarely used for the crushing of rocks above medium hardness.
However, with the rapid development of national engineering construction projects, such as highways, the requirements for pavement-specific stone are very strict. For example, the ultimate compressive strength of products must be greater than 100 MPa, and the particle-like flaky content must be less than 10%. Both jaw crushers and cone crushers are difficult to meet these requirements. This forced people to switch to hydraulic impact crushers. Therefore, under the conditions of hard rock production, the particle size of the hydraulic impact crusher varies with the structure shape of the crusher, the rotor speed, and the wear of the hammer. It improves the output of the product, reduces the degree of over-grinding, and improves the performance of the equipment. It has very important practical significance.
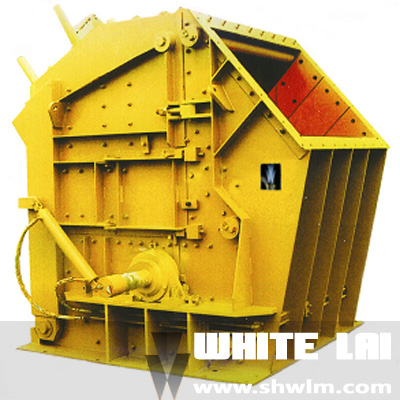
1 The impact of the type of crusher on the needle shape of the product The type of crusher has a great influence on the needle shape of the product. Taking the three types of crushers (颚, cone and impact type) which are widely used at present, as an example, the working principle of the crushed stone is different. According to the production practice, the crusher crushing machine uses the crushing between the two planes, so the needle-like crushed stone has the largest content (>15% -20%;) The cone crusher uses the crushing and breaking of the two arc faces. The needle-like crushed stone content is second (10%-15%;) and the impact type (including the counter-attack type). The crusher is broken by the impact force of the plate hammer and the counterattack plate in the crushing chamber, and the ore breaks along the weakest part of the surface energy. , gravel needles have the lowest content (
2 Impact of impact speed on product particle size The impact speed of hydraulic impact crusher (end hammer speed of plate hammer) has a great influence on product size, production capacity and plate hammer wear. In general, the increase of the impact speed (ie, the rotor speed) means that the hammer impact force, the counterattack force and the collision force between the materials are improved. Therefore, the product size will be finer and the crush ratio will be improved, but the hammer and The wear of the counterattack will also increase. At present, the general impact speed is 15-45m / s. When used as coarse crushing, the impact velocity should be taken as a small value. When used as a fine crush, it should be taken as a large value.
In addition, the determination of the impact velocity should also take into account the hardness of the rock. The harder the rock is, the smaller the brittleness is, and the higher the impact speed should be; otherwise, the lower it should be.
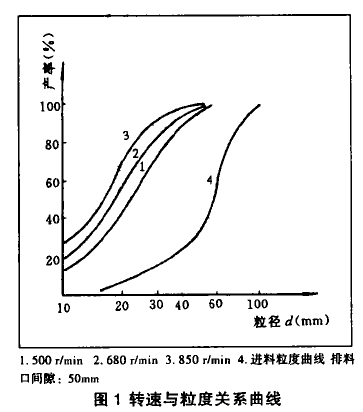
It can be seen from Fig. 1 that when the hydraulic impact crusher breaks hard rock, when the rotor speed is changed within the range of 500-850 r/min (ie, the blade edge line speed is 31-5 m / s), The product curve maintains similar particle size characteristics, ie the higher the rotor speed, the finer the product size. For the expressway, as the impact speed increases, the stone with the largest particle size d of 10~30mm has a small difference in proportion, but the content of stone powder is greatly increased, which means waste of raw materials and unnecessary energy. Excessive wear such as consumption and hammers. Therefore, the impact speed should not be excessively pursued. However, in other crushing industries where the grinding is a follow-up process, it is an effective way to increase the output and reduce the energy consumption within the acceptable range of wear such as the hammer.
In addition, it can also be seen from the figure that in the case of fine crushing in the case where the material hardness is large, although the impact speed is high, the average crushing ratio of the material is not large.
Impact of impact component shape on product size
1 Impact of the shape of the counterattack When the hydraulic impact crusher breaks the rock, it not only breaks by the impact of the hammer, but it is also important to break the impact of the hit rock on the counterattack. Therefore, the shape of the counterattack plate also plays an important role in material breakage. Different from other crushers of the same type, the counter-attack plate of the hydraulic impact crusher adopts a zigzag profile. As shown in Fig. 2, due to the impact of the rock on the serrated edge, it can generate a large counterattack force and local ratio. Pressure. In addition, since the facet of the sawtooth counterattack plate forms an inclination angle with the bottom surface of the counterattack plate, the residence time of the rock in the crushing cavity is increased. Therefore, the zigzag counterattack plate can significantly improve the material crushing ratio and the output. The particle size curve of the flat counterattack plate and the serrated counterattack plate is shown in Fig. 3. As can be seen from Fig. 3, under the same conditions. The use of the serrated surface counterattack plate has a finer product granularity than the planar counterattack plate, and the over-grinding phenomenon is also more serious. However, according to production statistics, the processing capacity can be increased by about 15% -25%.
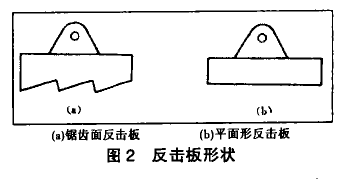
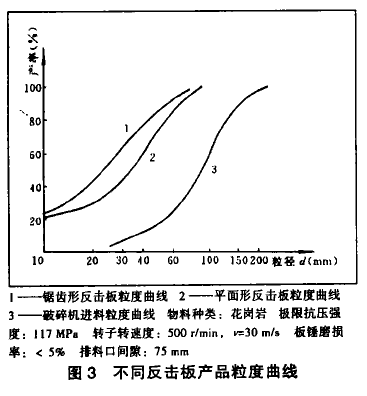
2. Influence of plate hammer wear The plate hammer is heavily worn, which is the main reason that affects the hydraulic impact crusher used for crushing. The PFC hydraulic impact crusher uses a long strip hammer with a symmetrical rectangular cross section (see Figure 4). The material is martensitic high chromium cast iron. However, when crushing granite with an ultimate compressive strength of 117 MPa, for every 1500 m3 of stone material with a diameter of 10-30 mm, the side of a single set of hammers is completely worn, with a daily working time. For 10 h, only about a week. In addition, the impact of the hammer wear on the product size change is also great. From the perspective of production practice, the product particle size is roughly proportional to the degree of wear of the hammer, that is, the more severe the hammer wear, the larger the product size; on the contrary, the smaller. This is because when the hammer is not worn, the edge of the hammer is in line contact with the rock, and the rock unit has the largest impact force and the strongest crushing capacity. The product has the finest particle size. After the hammer is worn, the contact between the rock and the hammer is gradually changed into surface contact. The larger the wear amount, the larger the contact surface, the smaller the impact force per unit area, the weaker the crushing ability, and the coarser the product granularity, although the impact speed of the counterattack is not large at this time. The relationship between the amount of hammer wear and product particle size is shown in Figure 5.
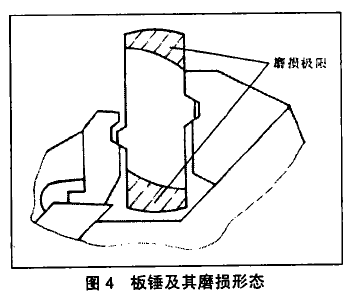
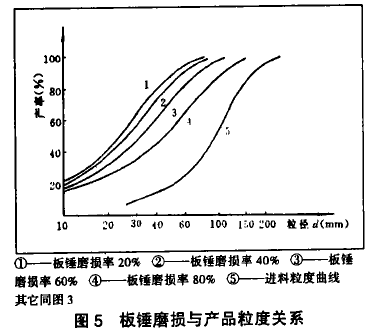
3. The influence of the gap of the discharge opening on the particle size of the product The gap of the discharge opening is the minimum clearance between the counterattack plate and the plate hammer. It is generally believed that the maximum particle size of the product of a hydraulic impact crusher should be determined by the size of the gap. In fact, this is the case when the hammer is not worn or the amount of wear is small. This is because the material crushed by the hydraulic impact crusher is generally cuboidal. When the impact energy is sufficient, the material entering the crusher will be fully broken, and few large stones will be extruded out of the discharge port. However, when the hammer is worn more seriously, the situation is different if the wear amount is greater than 60%-70%. At this time, the impact force of the contact surface between the rock and the hammer will be greatly reduced, and a considerable part of the material cannot be broken in time. Since the counter-attack plate of the general hydraulic impact crusher is equipped with a safety device to prevent the material that is not easily broken (such as cast iron) from damaging the crusher after entering, the part of the material will be raised by the high-speed rotating rotor to raise the counter-attack plate. And extruded from the discharge opening. At this time, the smaller the gap of the discharge opening is, the larger the frequency and amplitude of the jump on the counter-attack plate. According to our production practice, when the discharge gap is 40-50mm, the maximum blockage of the discharged rock can reach 140~150mm. In severe cases, the pulley belt will be burned and the material will completely block in the crushing chamber and the production will be stopped. When the product is an engineering specification stone, the gap of the discharge opening of the crusher should be reasonably determined according to the feed particle size. According to the production practice, when the average particle size of the feed is about 120mm, and the new plate hammer and counterattack plate, the gap of the discharge port is generally 100-200mm, so as to reduce the over-grinding phenomenon of the product, and obtain a better particle size composition range and comparison. High product yield. Then, with the hammer wear, the discharge gap is gradually reduced; while the feed particle size is about 180 mm, and the same is the new plate hammer and the counterattack plate, the gap of the discharge opening is generally 80-100 mm to obtain a better particle size composition. After that, the size is generally maintained to prevent the blockage phenomenon after the hammer is worn. Rocks larger than the specification stone range are sieved and then crushed.
in conclusion:
1 The hydraulic impact crusher has the least amount of product needle-like content, and when crushed granite, its content is less than 5%.
2 Sawtooth counterattack plate helps to increase the material crushing ratio, and the output will increase by 15% to 25%.
3 Plate hammer wear has a great influence on the particle size of the product, and its particle size is roughly proportional to the wear of the plate hammer.
4 The maximum particle size of the product does not depend entirely on the size of the discharge opening; the reasonable discharge opening size should be determined according to the degree of wear of the hammer and the particle size of the feed.
Reprint, please indicate the source, Shanghai Yuli Road and Bridge Equipment Co., Ltd. http://://news.chinawj.com.cn Editor: (Hardware Business Network Information Center) http://news.chinawj.com.cnLed Therapy Bulb
Led therapy bulb with E27/E26 socket, Red Light Infrared works for full body, we have 12w 24w 36w bulb, with 660nm and 850nm wavelength, customized led also ok.
The most convenient red light therapy solution
-
E27 therapy bulb Suitable to use on any part of the body.
-
Anything in the first couple of inches of skin can be affected by this light, making it suitable for; hair health, general skin tone/beauty, acne, eczema, wounds, bruises, sunburn, joint pain, wrinkle prevention, and much more.
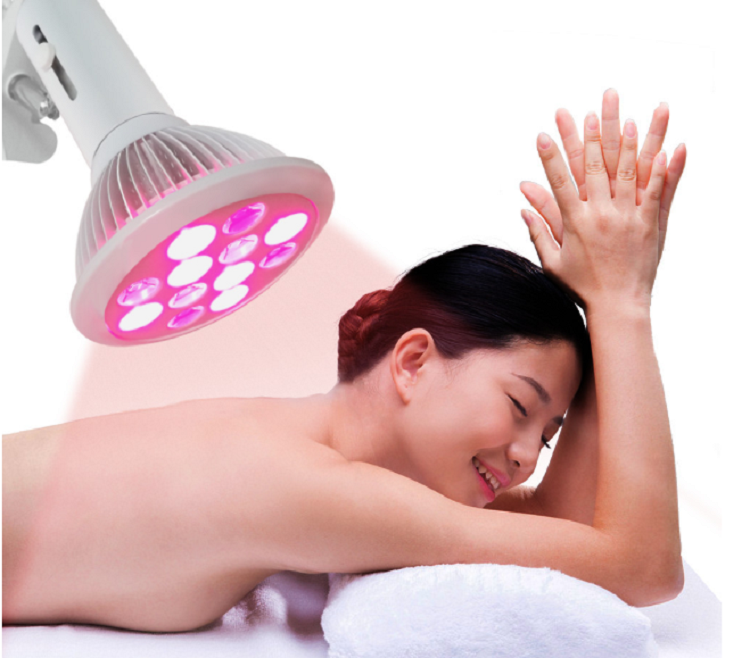